Understanding Precision Injection Moulding in Metal Fabrication
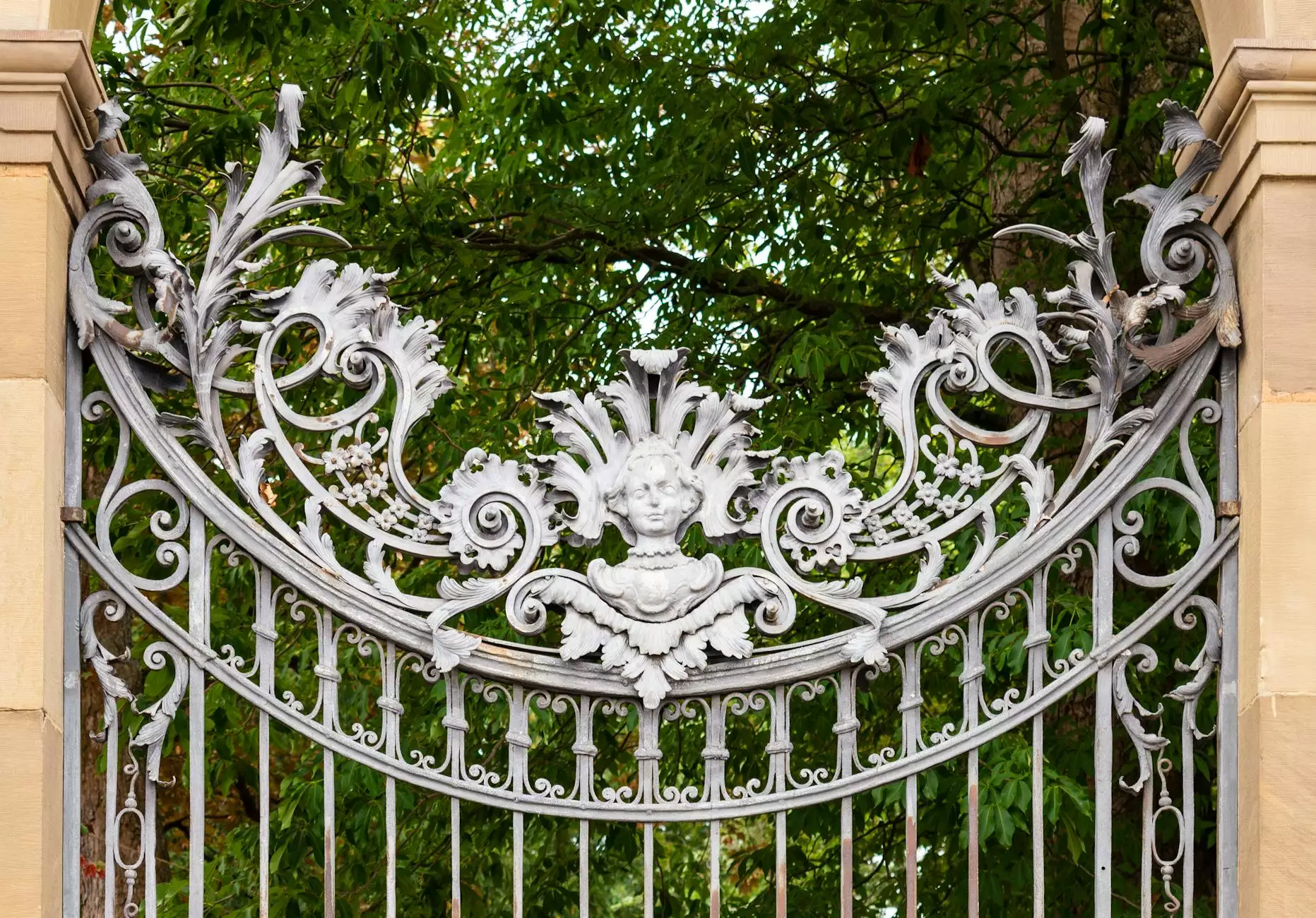
Precision injection moulding is a transformative technology in the realm of manufacturing, providing unparalleled accuracy and efficiency. As industries continue to evolve, the demand for high-quality metal fabrication grows, and precision injection moulding emerges as a pivotal solution.
What is Precision Injection Moulding?
Precision injection moulding refers to a manufacturing process that involves injecting molten material, typically thermoplastic or thermosetting polymers, into a mould to create intricate shapes with fine details. This method allows for the production of complex geometries that are not only consistent in quality but also offer enhanced durability.
Key Features of Precision Injection Moulding
- High Dimensional Accuracy: Components produced through this method often exhibit a high degree of dimensional precision, which is essential in industries that demand tight tolerances.
- Rapid Production Cycle: The speed of precision injection moulding facilitates quick turnaround times, enabling manufacturers to meet market demands efficiently.
- Material Versatility: A wide range of materials can be employed in this process, from various types of plastics to metal composites, making it adaptable to different project requirements.
- Minimized Waste: The process is designed to recycle excess material effectively, reducing waste and lowering production costs.
The Role of Precision Injection Moulding in Metal Fabrication
In the field of metal fabrication, precision is not merely an advantage; it is a requirement. With the growing complexity of designs and applications, incorporating precision injection moulding into metal fabrication processes helps achieve superior results. Here are several aspects where this method shines:
Enhanced Product Quality
Components manufactured via precision injection moulding exhibit superior surface finishes and reduced roughness, which is critical for metal parts used in intricate assemblies. This attention to detail translates to enhanced product quality and customer satisfaction.
Cost-Effectiveness
Utilizing precision injection moulding can significantly reduce production costs. By minimizing material waste and shortening cycle times, manufacturers can achieve greater profit margins while maintaining high standards.
Innovation and Customization
The flexibility of precision injection moulding allows designers and engineers to innovate without limitations. Custom shapes and configurations can be engineered to meet the specific needs of clients across various sectors, including automotive, aerospace, and medical applications.
Applications of Precision Injection Moulding in Different Industries
Across various industries, precision injection moulding offers applications that redefine how parts are produced and used. Below are some of the key sectors that benefit from this process:
Aerospace Industry
In aerospace, where safety and reliability are paramount, precision injection moulding is utilized for manufacturing components that meet strict regulatory standards while offering weight savings and enhanced performance.
Automotive Sector
The automotive industry utilizes precision injection moulding for producing lightweight yet sturdy parts that contribute to fuel efficiency and lower emissions. Components such as dashboards, internal panels, and various precision-engineered parts are produced using this method.
Medical Devices
The production of medical devices demands the highest quality, and precision injection moulding provides the required reliability. Surgical tools, imaging equipment, and housing for delicate instruments are often crafted with this advanced method.
Consumer Electronics
With the rapid development in consumer technology, electronic devices benefit greatly from precision injection moulding. From smartphone casings to intricate internal components, this process can produce fine detail and a smooth finish.
The Process of Precision Injection Moulding
Understanding how precision injection moulding works is essential for metal fabricators looking to integrate this technique into their operations. The process involves several critical steps:
1. Material Selection
Choosing the right materials is pivotal. Depending on the end-use, options may range from thermoplastics to metal alloys. Each material has its characteristics that need to be assessed for compatibility with the injection moulding process.
2. Mould Design
The design of the mould dictates the final part's quality. Precision in mould fabrication is crucial, as it directly affects the dimensional accuracy and surface finish of the components produced.
3. Injection Phase
During this stage, the heated material is injected into the prepared mould at high pressure. This step is where precision really comes into play, as the speed and temperature need to be controlled meticulously to avoid defects.
4. Cooling and Solidification
Once the material has been injected, it is allowed to cool and solidify within the mould. Cooling time is essential and depends on various factors including material type and mould design. This phase critically influences the final dimensions and physical properties of the product.
5. Ejection and Finishing
After cooling, the finished part is ejected from the mould. Additional finishing processes may include trimming, polishing, or coating to meet specific requirements for functionality and aesthetics.
Benefits of Choosing Precision Injection Moulding Over Traditional Methods
When considering manufacturing options, precision injection moulding provides numerous benefits over more traditional methods:
- Increased Repeatability: Consistency in production is enhanced, as high precision reduces the risk of variation between batches.
- Greater Design Freedom: This method supports complex designs that are often not feasible with conventional techniques like machining.
- Improved Performance: The mechanical properties of the injected parts can be superior due to optimized production conditions.
- Streamlined Production Processes: Faster production cycles minimize lead times and improve time-to-market for new products.
Challenges in Precision Injection Moulding
Though precision injection moulding offers considerable advantages, there are challenges that must be addressed:
1. Initial Setup Costs
While precision injection moulding can reduce long-term costs, initial setup costs for mould creation and machine calibration can be substantial. This requires careful planning and investment.
2. Complexity in Tooling
Designing and fabricating the mould can be complex, requiring skilled expertise. Improper tooling can lead to defects, waste, and increased production time.
3. Material Limitations
Although versatile, not all materials are suitable for this process. Understanding the limitations and selectivity of materials is crucial for ensuring product quality.
Conclusion
In summary, precision injection moulding stands out as a superior manufacturing technique for metal fabricators looking to enhance productivity and quality. The ability to create intricate designs with minimal waste, alongside the potential for customization, makes it an invaluable asset in today’s competitive landscape. At deepmould.net, we are dedicated to leveraging cutting-edge technology in precision injection moulding to deliver the best products to our clients. Embrace this advanced manufacturing process and join the movement towards precision and efficiency in your operations.
For more information and insights into precision injection moulding and how it can benefit your business, visit deepmould.net.